High Purity Gas Systems
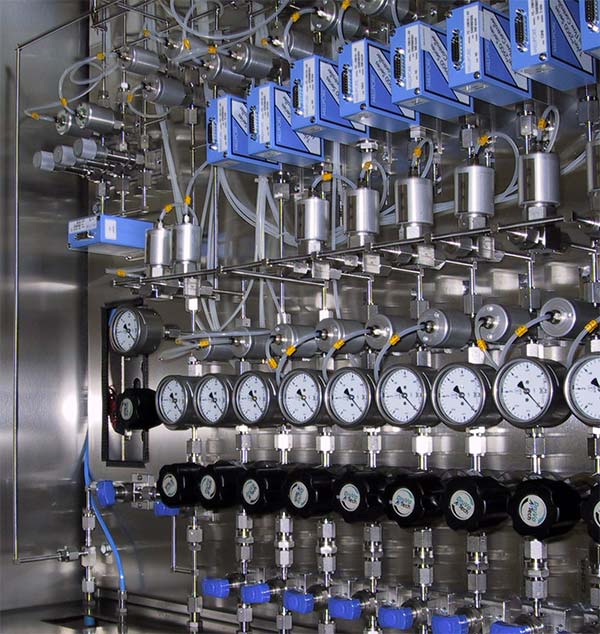
Gas control system for high purity gases are used whenever there is a high demand on the cleanliness of the gases. Due to the construction of the system and selection of the components these systems fulfil the specification regarding leak tightness and durability for very critical gases, such as corrosive and toxic gases.
Common applications for high purity gas systems are processes for the deposition of thin layers in CVD process, such as LPCVD in low pressure applications or as in atmospheric pressure deposition. Materials such as silicon wafers, glass, plastic, metal, etc. are used as substrates for the deposition. Other applications are the formation of synthetic ceramics or synthetic quartz or any other processes where the characteristics of a surface are modified, such as in a sputter process.
The central part of SIGAs gas control systems are MFCs, mass flow meters and controllers. The detected physical measurement is based on the transport of heat across the sensor element. Physical properties of the gas alongside the number of gas molecules influence the result. As a result, a true mass flow is measured. The units are calibrated to show litre/minute based on standard conditions at 0°C and 1013 hPa. Conversion factors can be used when different gases flow across the unit.
Other important components of our gas mixing units are valves, either diaphragm or bellow sealed. The valves are usually pneumatically activated, normally closed or normally open. Valves at the system inlet or purge valves may also be manually operated. As another option, solenoid valves can be used. To complete the system we add pressure regulators, pressure gauges and transmitters, check valves, etc. Components are always selected according to the requirement of each application.
Stainless steel tubes are used throughout the system, internal surface roughness 0.4 μm, SS-316 or SS-316L, corresponding to material-nr. 1.4404 or 1.4435. Electro-polished tubes are used on request, internal surface roughness 0.25 μm.
All tube connections are orbital welded under inert gas. Tube bends are replaced by machined elbows. Where parts need to be removed we use compression fittings or face seal fittings, e.g. Swagelok and VCR-fittings or compatibles. For the face seal fittings we use stainless steel gaskets, with or without silver plating.
Gas control systems are built into a steel enclosure with powder coating or in a stainless steel enclosure. In some cases mounting is required on a mounting plate. Systems are then integrated in the customer's system.
For system control SIGA offers programmable controllers with a touch screen for visualisation and operator interaction. As an alternative all signals can be wired to a bus coupler with Profibus DP or another serial interface for communication with the system's upstream controller. As another option all signals can also be wired to a terminal strip or a connector for connection with the system's controller.