Precursor Vaporizer System
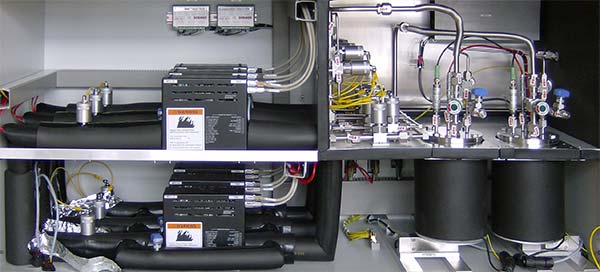
You can see galleries with our Vaporizer Systems on the following pages:
Vaporizer Systems are used to control the mass flow of a liquid precursor to a CVD deposition process. Vaporization and mass flow control is done by a system for the direct vaporization without carrier gas.
Typical applications are the control of silanes, chlorides and metalakyles such as SiCl4, TiCl4, SiHCl3, HMDSO, DEZ or TMA. Also solvents and water are within the range of applications. The vaporizer systems are often used in VCD processes for the deposition of thin layers out of a gas phase, usually at low pressures LPCVD and/or enhanced by plasma PECVD. Other applications are at atmospheric pressure such as in a flame hydrolysis FHD. In this case the flame control will be part of the system.
One of the characteristics of SIGAs vaporizer systems is next to the vaporization without carrier gas, the possibility to supply the vapour flow to several points of use. It is possible to provide vapour flow to several deposition systems at the same time or to several inlets at one process chamber.
The possibility to feed several processes out of one single vaporizer offers the option for cost reduction. A number of components and control elements can be spared and mounting space can be reduced. Another option is the integration of 2 vaporizer systems within one control system.
- Vaporizer for one precursor
- Vaporizer system for 2 or more precursors
- Liquid flow control with subsequent vaporisation
The precursor is filled into a stainless steel container, the evaporator, and heated to the desired vaporization temperature. The mass flow of the gas phase is directly controlled by a mass flow controller (MFC) and fed to the process. A carrier gas such as used in a bubbler or mixer is not required. All other gas flows required for the process can therefore be adjusted independent of the required flow of vaporized precursor.
The vaporizer system is metal sealed, elastomeres are not used within the system, and thereby fulfilling a main requirement for a safe system. System design is according to customer specification to meet the requirements of the application. Temperature of the evaporator is selected according to the process pressure and vapour pressure of the precursor; it can reach up to 80°C or up to 140°C.
Pressure and temperature are constantly monitored. Power to the heater of the evaporator is switched off at over-pressure or over-temperature. All components in contact with precursor vapours are heated. A line heater for the tube to the point of use is supplied when required by actual line pressure.
All components and tubes in contact with the precursor are made of stainless steel, SS-316L, equivalent to material-nr. 1.4404. Leak tightness is one of our main issues. Orbital welding under inert gas is used for tube connections. Face seal fittings, e.g. Swagelok VCR are used where necessary.
The evaporator can be refilled automatically during a running process. The precursor is supplied in a bulk container and pressurised with inert gas. Via a dip tube the liquid will flow to the evaporator. Please have a look at our Precursor Refill System.
A programmable controller with a 12” touch-screen for visualisation and operation is applied to control all system functions such as temperature control, automatic refill, etc. MFC set-point and the desired flow path are selected by the upstream controller of the deposition system. Communication via Profibus-DP or an other serial interface. Details for the control such as operator interaction, manual control and interlocks with the upstream system are designed according to process requirements.
The vaporizer system is mounted in a customized or a standard steel housing. Vaporizer and control system can be installed in one or in two separate housings. Enclosure is designed to allow integration in the deposition system or adjustment to the requirements at the point of installation.